Lph Reverse Osmosis Plants
- 250 Liters Per Hour Ro Plant System
- 500 Liters Per Hour Ro Plant System
- 1000 Liters Per Hour Ro Plant System
- 5000 Liters Per Hour Ro Plant System
250 Liters Per Hour Reverse Osmosis Plant System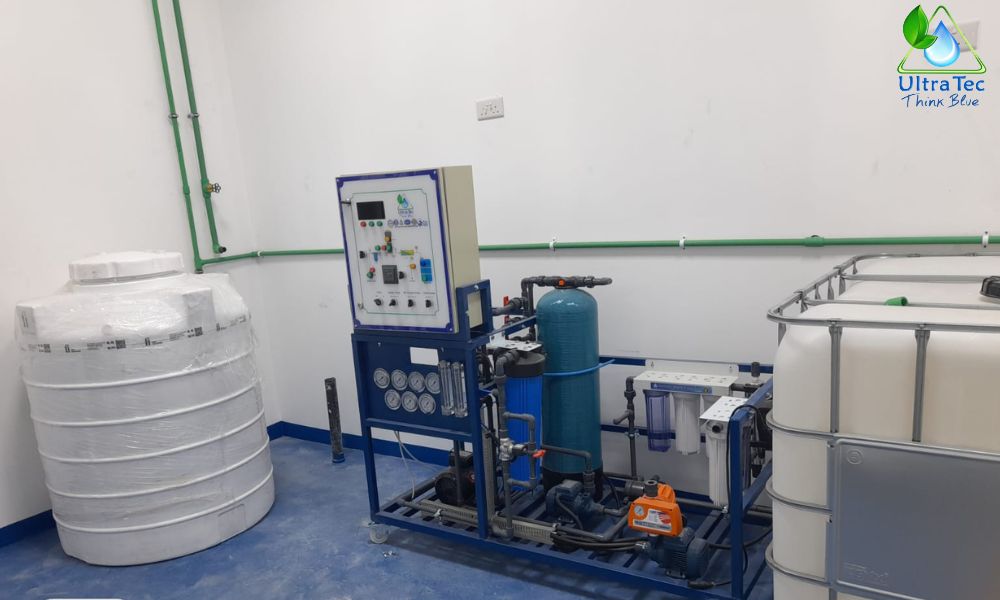
Designing a Reverse Osmosis (RO) system with a capacity of 250 liters per hour (LPH) involves careful planning and consideration of various components to achieve optimal performance and water quality. The process begins with pre-treatment, which is essential for protecting the RO membrane from potential damage and fouling. This pre-treatment stage typically includes a sediment filter to remove particles like sand and silt, a carbon filter to eliminate chlorine and organic compounds, and possibly a water softener if the water is hard. These steps are crucial to ensure the longevity and efficiency of the RO membrane.
At the core of the system is the RO membrane module. This component uses high pressure to force water through a semi-permeable membrane, effectively removing contaminants and producing purified water. To achieve the necessary pressure, usually between 8-12 bar, a high-pressure pump is required. This pump is vital for driving the filtration process and ensuring the system operates effectively. Additionally, the system is equipped with a storage tank to hold the purified water, and may include post-treatment steps such as UV sterilization and polishing filters to ensure the water meets the highest purity standards.
The system’s performance is monitored and managed through a control mechanism that includes pressure gauges, flow meters, and automatic shut-off valves. These components are crucial for maintaining system efficiency and ensuring the RO system operates within its designed parameters. The design also takes into account the quality and source of the feed water, as these factors influence the selection of the RO membrane and the pre-treatment requirements. The system’s recovery rate, typically between 50% and 75%, determines the volume of feed water needed to produce the desired 250 LPH of purified water. For instance, with a 60% recovery rate, approximately 417 LPH of feed water is required.
Proper installation of the RO system involves setting up the components in an appropriate environment and conducting thorough testing to ensure functionality and compliance with water quality standards. Routine maintenance is critical for the system’s long-term operation, including regular replacement of pre-treatment filters, cleaning or replacing the RO membrane, and performing system checks to prevent leaks and ensure smooth operation. Following safety protocols and adhering to regulatory standards are essential to guarantee both the effectiveness and safety of the RO system.
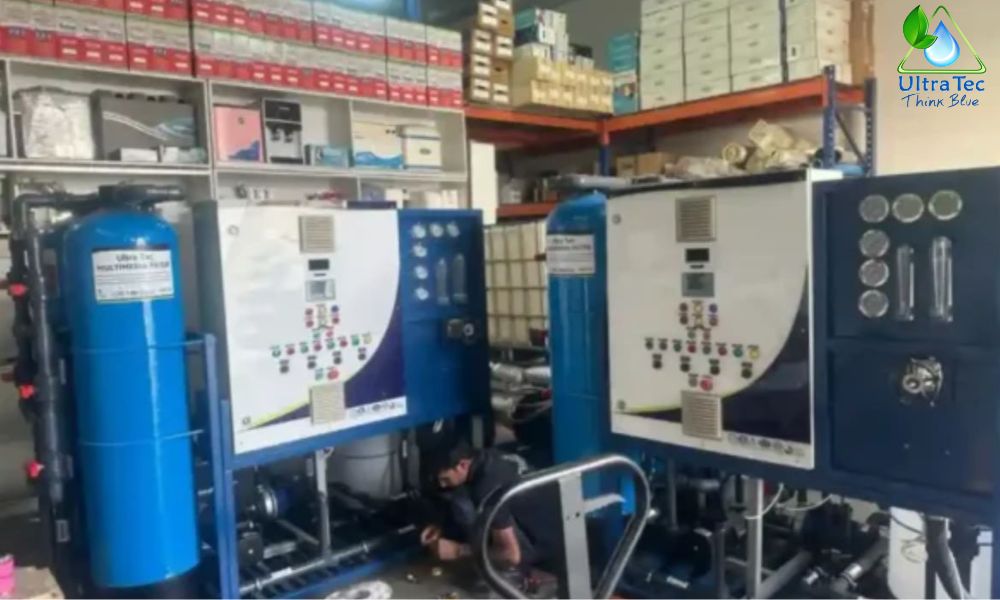
Designing a 500 liters per hour (LPH) Reverse Osmosis (RO) system for treating water with an initial concentration of 1000 parts per million (ppm) requires careful planning and attention to key components to achieve effective water purification. The process starts with pre-treatment, which is essential to protect the RO membrane from potential damage caused by contaminants. In this stage, sediment filters are used to remove suspended solids, while carbon filters eliminate chlorine and organic substances that could degrade the membrane.
ِThe heart of the system is the RO membrane module. This component relies on high-pressure pumps to force water through a semi-permeable membrane. The membrane is designed with a high rejection rate, meaning it effectively separates water from impurities, significantly reducing the concentration of contaminants. For a system with a capacity of 500 LPH, the high-pressure pump must provide sufficient pressure, typically between 8-12 bars, to ensure the membrane operates effectively.
ِThe system design also includes a product water storage tank to collect and store the purified water, as well as a concentrate outlet to dispose of the rejected contaminants. Additionally, post-treatment options, such as UV sterilizers and polishing filters, may be incorporated to further enhance the quality of the purified water, ensuring it meets the highest standards.
ِTo maintain optimal performance, the system is equipped with precise control mechanisms, including pressure gauges, flow meters, and automatic shut-off valves. These tools are essential for monitoring and regulating the system’s operation. The recovery rate, which represents the proportion of purified water extracted from the total feed water, typically ranges from 50% to 75% in RO systems. For a 500 LPH output with a 60% recovery rate, approximately 833 LPH of feed water is required.
ِRegular maintenance is crucial to ensure the system continues to operate smoothly. This includes changing pre-treatment filters, cleaning or replacing the RO membrane, and checking all components to ensure they are functioning properly. By following this comprehensive approach, the RO system can effectively reduce the initial 1000 ppm concentration to a much lower level, producing high-quality purified water.
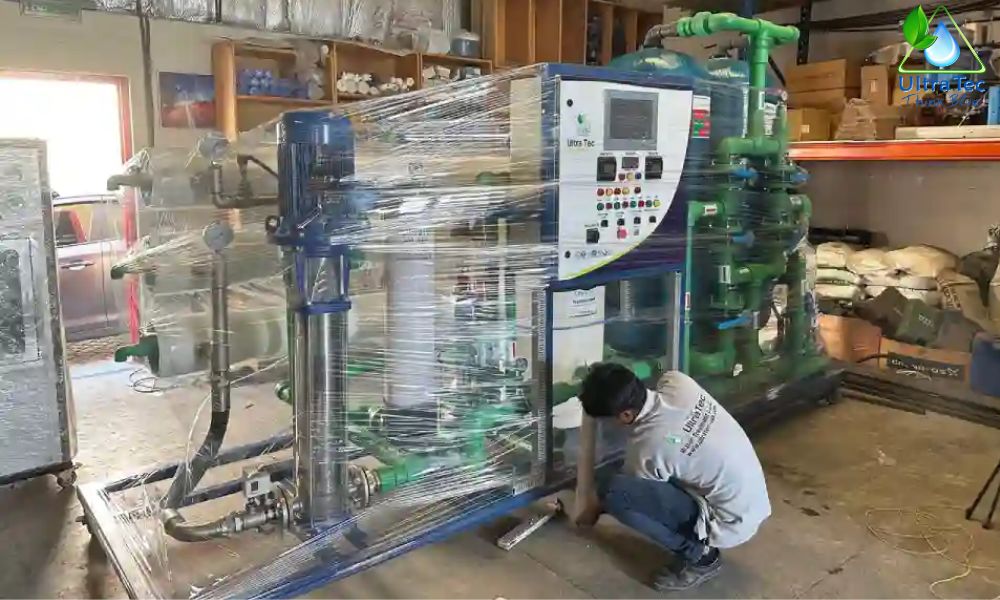
A 1000 liters per hour (LPH) Reverse Osmosis (RO) system is engineered to efficiently process large volumes of water through multiple filtration stages. The process begins with pre-treatment, where sediment and carbon filters are used to eliminate particulates and chlorine, safeguarding the RO membrane from potential damage. The core component, the RO membrane, is powered by a high-pressure pump that effectively filters out dissolved impurities, significantly reducing contaminants in the water.
To achieve the desired 1000 LPH output, the system typically operates with a recovery rate between 50% and 75%, meaning it requires a larger input of feed water. Post-treatment options, such as UV sterilization, may be added to ensure the purified water meets stringent quality standards. Regular maintenance, including the timely replacement of filters and the RO membrane, is essential to maintain the system’s optimal performance and extend its lifespan.
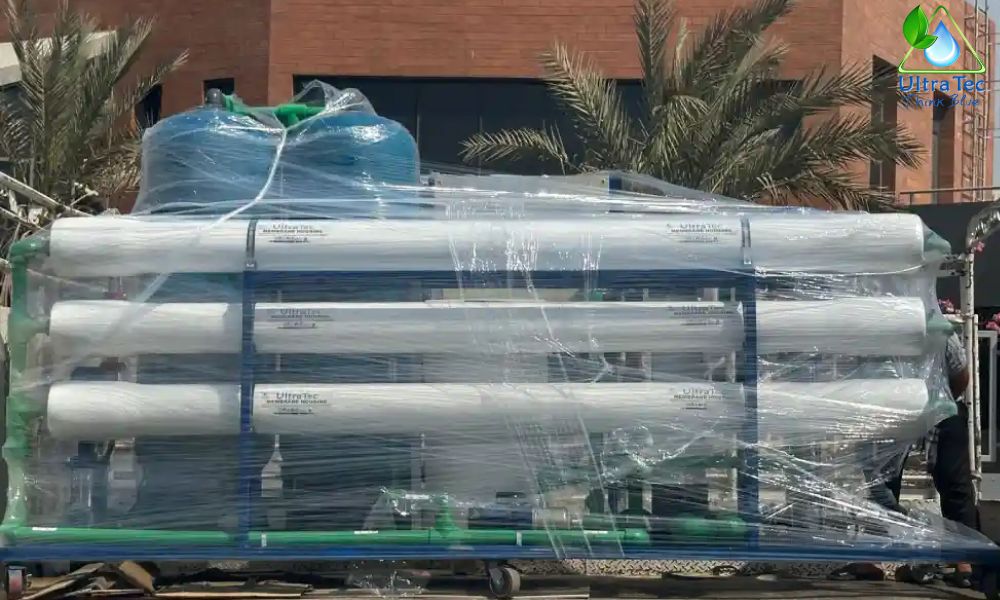
A 5000 liters per hour (LPH) Reverse Osmosis (RO) system is specifically designed to efficiently purify large volumes of water. The process begins with pre-treatment, which typically involves sediment filters to remove larger particles and carbon filters to eliminate chlorine and organic contaminants, thus protecting the RO membranes from damage.
The system employs a high-pressure pump to generate the necessary pressure, usually between 8-12 bars, to push water through the RO membranes. These membranes, often arranged in multiple stages or parallel configurations, are highly effective at separating impurities, allowing only purified water to pass through. Given a typical recovery rate of 50% to 75%, the system requires a substantial amount of feed water to achieve the 5000 LPH output of clean water.
To further enhance water quality, post-treatment steps such as UV sterilization or additional polishing filters may be added. Proper maintenance is crucial for the system’s long-term efficiency and includes regularly replacing pre-treatment filters, cleaning or replacing the RO membranes, and closely monitoring system components like pressure gauges and flow meters. This comprehensive approach ensures the RO system operates efficiently, delivering consistent, high-quality purified water.