600 LPH Reverse Osmosis System
In regions across Africa where access to clean water can be a challenge, a reliable water treatment solution is crucial. The 600 LPH (liters per hour) reverse osmosis system, designed to handle water with 1000 ppm (parts per million) of contaminants, offers a robust and efficient solution for ensuring high-quality water purification. This advanced system integrates several key components to deliver optimal performance.
The setup includes a media vessel for initial filtration, effectively removing larger particles and extending the lifespan of the subsequent components. The feed pump ensures a consistent flow of water into the system, while the high-pressure pump drives water through the reverse osmosis membranes with sufficient force to achieve thorough purification.
At the heart of the system are three 4-inch membrane vessels, each housing three reverse osmosis membranes. These membranes are critical for separating impurities from the water, providing reliable filtration even in challenging conditions. A bag filter is incorporated to capture fine sediments and protect the membranes from potential damage.
1. Media Vessel
Function: The media vessel serves as the initial stage of filtration, designed to remove larger particles and sediments from the incoming water. This pre-filtration process helps protect the downstream components of the RO system, ensuring longer operational life and better performance.
Importance: By removing larger debris, the media vessel reduces the load on the subsequent filtration stages and improves overall system efficiency.
2. Feed Pump
Function: The feed pump is responsible for maintaining a consistent flow of water into the reverse osmosis system. It ensures that the water pressure is adequate for the high-pressure pump and the filtration process.
Importance: A steady flow of water is crucial for the effective operation of the RO system, enabling it to process the desired volume of water per hour.
3. High-Pressure Pump
Function: This pump generates the necessary pressure to push the water through the reverse osmosis membranes. The high-pressure pump is essential for overcoming the osmotic pressure of the water and ensuring effective contaminant removal.
Importance: High pressure is critical for the efficiency of the reverse osmosis process, allowing the system to handle high levels of contaminants.
4. Membrane Vessels
Configuration: The system includes three 4-inch membrane vessels, each housing three reverse osmosis membranes. These vessels are designed to accommodate the membranes and provide a stable environment for the filtration process.
Membrane Details: Each vessel contains three membranes, which work in series to ensure thorough filtration and removal of contaminants.
Importance: The use of multiple membranes increases the system's capacity and effectiveness, enabling it to handle higher contaminant loads and produce cleaner water.
5. Bag Filter
Function: Positioned before the water reaches the reverse osmosis membranes, the bag filter captures fine sediments and particles. This pre-filtration step helps protect the membranes from clogging and damage.
Importance: The bag filter enhances the longevity and performance of the RO system by preventing debris from reaching the sensitive membrane surfaces.
6. Pressure Control Mechanisms
Low-Pressure Switch: Monitors and maintains the minimum operational pressure required for the RO system to function effectively. It ensures that the system does not operate below optimal pressure levels.
High-Pressure Switch: Protects the system by monitoring and controlling the maximum pressure, preventing damage to the components and ensuring safe operation.
Importance: Proper pressure control is essential for the reliable and efficient performance of the RO system, preventing operational issues and prolonging the lifespan of the equipment.
7. Control Panel
Function: The control panel provides a user-friendly interface for managing and monitoring the reverse osmosis system. It allows operators to adjust settings, view operational status, and perform maintenance tasks.
Importance: The control panel simplifies the management of the RO system, enabling easy adjustments and real-time monitoring to ensure optimal performance.
Applications and Benefits
1. Tailored for African Water Challenges
Context: In many regions of Africa, water sources may contain high levels of contaminants, making effective water treatment essential for health and safety.
Benefit: The 600 LPH RO system is specifically designed to address these challenges, providing a reliable solution for producing clean and safe drinking water.
2. Reliable Purification
Performance: The system’s advanced components and high capacity ensure efficient removal of contaminants, delivering purified water suitable for various applications.
Versatility: Suitable for use in municipal water systems, industrial processes, and other settings where high-quality water is required.
3. Cost-Effective and Durable
Longevity: The robust design and quality components of the RO system contribute to its durability and long-term performance, reducing maintenance costs and extending service life.
Efficiency: By providing effective water treatment with minimal operational costs, the system offers a cost-effective solution for water purification needs.
Maintenance Tips for 600 LPH Reverse Osmosis System at 1000 ppm
1. Regular Inspection and Cleaning
Routine Checks:
- Frequency: Inspect the system components monthly.
- Checklist: Examine the media vessel, feed pump, high-pressure pump, membrane vessels, and bag filter for signs of wear or damage.
Cleaning Procedures:
- Media Vessel: Periodically clean or replace the media to prevent clogging and ensure effective pre-filtration.
- Bag Filter: Replace or clean the bag filter as needed to maintain optimal flow and prevent pressure drop.
2. Membrane Maintenance
Membrane Cleaning:
- Frequency: Clean the reverse osmosis membranes every 6 to 12 months, or as needed based on water quality and system performance.
- Procedure: Use appropriate membrane cleaning solutions and follow manufacturer guidelines to avoid damage.
Membrane Replacement:
- Frequency: Replace membranes every 2 to 3 years, or when performance declines significantly.
- Signs: Reduced flow rate, increased pressure, or declining water quality indicate the need for replacement.
3. Monitoring and Managing Pressure
Pressure Checks:
- Frequency: Regularly monitor pressure levels using the low and high-pressure switches.
- Actions: Ensure that the system operates within the recommended pressure range. Adjust the high-pressure pump settings if necessary.
Pressure Switch Maintenance:
- Inspection: Check pressure switches for proper operation and calibration.
- Adjustment: Ensure that switches are correctly set to prevent system damage and maintain efficient operation.
4. System Sanitization
Disinfection:
- Frequency: Sanitize the entire system every 6 to 12 months to prevent microbial growth and contamination.
- Procedure: Use appropriate disinfectants and follow manufacturer recommendations for cleaning and sanitizing procedures.
Flush System:
- Procedure: Flush the system with clean water after sanitization to remove any residual disinfectant.
5. Control Panel Care
Inspection:
- Frequency: Regularly inspect the control panel for signs of malfunction or error messages.
- Actions: Ensure that all indicators and alarms are functioning correctly and respond to any alerts promptly.
Calibration and Testing:
- Procedure: Periodically test and calibrate the control panel settings to ensure accurate monitoring and control of the system.
6. General Maintenance Practices
Documentation:
- Record Keeping: Maintain detailed records of maintenance activities, including inspections, cleaning, and replacements.
- Benefits: Accurate records help track system performance and identify trends or recurring issues.
Training and Safety:
- Training: Ensure that personnel operating and maintaining the system are properly trained.
- Safety: Follow safety guidelines and procedures to prevent accidents and ensure safe operation of the system.
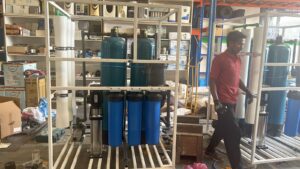
How a 600 LPH Reverse Osmosis System at 1000 ppm Works
1. Water Intake
Source Water: The system starts by drawing water from a source, which has a contamination level of up to 1000 ppm.
Feed Pump: The feed pump is responsible for moving the incoming water into the system at a consistent flow rate. It ensures that the water pressure is adequate for the subsequent filtration stages.
2. Initial Filtration
Media Vessel:
- Function: The water first passes through a media vessel, which contains filtration media designed to remove larger particles, sediments, and debris.
- Purpose: This pre-filtration step protects the downstream components from clogging and damage, and improves the overall efficiency of the RO system.
3. Pre-Filtration
Bag Filter:
- Function: Positioned after the media vessel, the bag filter captures finer sediments and particulates that were not removed by the media vessel.
- Purpose: This ensures that only clean water flows into the reverse osmosis membranes, preventing them from becoming clogged or damaged.
4. High-Pressure Pumping
High-Pressure Pump:
- Function: The high-pressure pump increases the water pressure to levels required for reverse osmosis. This pressure is necessary to overcome the natural osmotic pressure of the water and force it through the RO membranes.
- Purpose: High pressure is critical for the effective operation of the RO process, enabling the system to handle water with high levels of contaminants.
5. Reverse Osmosis Filtration
Membrane Vessels:
- Configuration: The system includes three 4-inch membrane vessels, each containing three reverse osmosis membranes. The membranes are the core component of the system, where the actual purification occurs.
- Function: Water is forced through the membranes, which have very fine pores that allow water molecules to pass while blocking contaminants, such as salts, bacteria, and other impurities.
- Process: The RO membranes separate the water into two streams—permeate (clean water) and concentrate (reject water with contaminants).
6. Post-Filtration
Permeate Water:
- Function: The clean water that passes through the membranes (permeate) is collected and is typically directed to a storage tank or point of use.
- Quality: This water is significantly purified, with contaminants reduced to a much lower level compared to the original 1000 ppm.
Concentrate:
- Function: The concentrated waste (reject water) containing the removed contaminants is expelled from the system.
- Disposal: This waste is usually directed to a drain or another disposal system.
7. Monitoring and Control
Control Panel:
- Function: The control panel manages the operation of the entire system. It includes sensors and switches to monitor pressure, flow rates, and other critical parameters.
- Adjustments: Operators can adjust settings and respond to alerts to ensure the system operates efficiently and safely.
Pressure Switches:
- Low-Pressure Switch: Monitors and maintains minimum pressure levels required for effective operation.
- High-Pressure Switch: Protects the system by monitoring maximum pressure to prevent damage and ensure safe operation.
8. System Maintenance
Routine Checks: Regular maintenance tasks, such as cleaning or replacing the media vessel, bag filter, and RO membranes, are essential to keep the system running smoothly and efficiently.
Sanitization: Periodic disinfection and flushing of the system help prevent microbial growth and ensure high water quality.
Conclusion
The 600 LPH reverse osmosis system, designed to handle water with up to 1000 ppm of contaminants, offers a powerful and reliable solution for achieving high-quality water purification. This advanced RO system is ideal for various applications, whether residential, commercial, or industrial, ensuring a consistent supply of clean and safe drinking water. With a capacity of 600 liters per hour, it effectively addresses challenging water conditions by significantly reducing impurities and improving overall water quality.
Featuring a multi-stage filtration process, including a media vessel and bag filter for pre-filtration, a high-pressure pump for optimal membrane performance, and three 4-inch membrane vessels, this system ensures thorough purification. The reverse osmosis membranes are crucial for removing contaminants, delivering purified water efficiently. The system’s user-friendly control panel and pressure switches allow for easy monitoring and adjustment, enhancing operational efficiency and user experience.
Investing in the 600 LPH RO system means choosing a reliable, cost-effective water treatment solution that meets demanding water quality needs. To explore how this advanced reverse osmosis system can benefit your specific application, contact us today for more information, a detailed quote, or to schedule a demonstration. Enhance your water purification process with our state-of-the-art 600 LPH system and enjoy the benefits of superior water quality.
Reviews
There are no reviews yet.